MISSION
DEFINITION
AIRBUS Defence and Space GmbH
ContributorsAIRBUS Defence and Space SAS, AIRBUS Defence and Space LTD, GMV, SPACEAPPS, SENER Aeroespacial, DFKI, ISISPACE
01
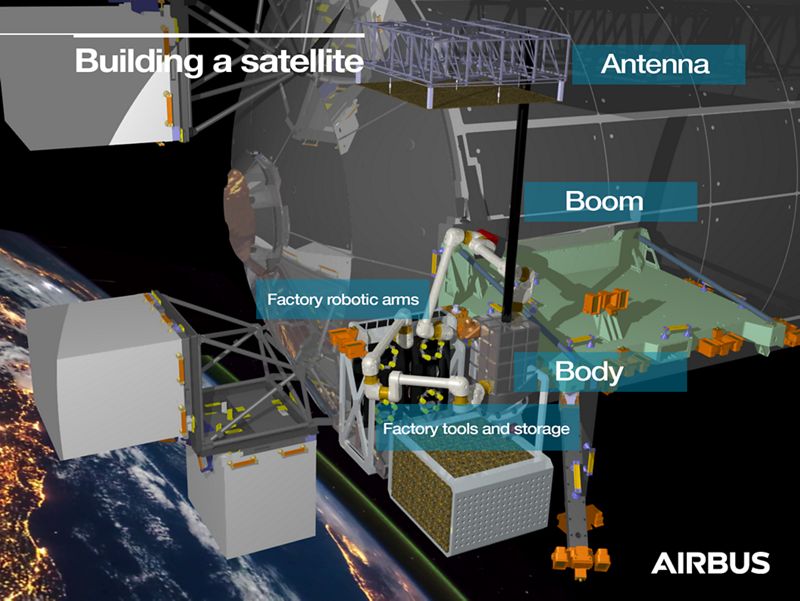
Highlights Summary
The initial baseline for the PERIOD demonstration mission has been developed and presented at the Mission Definition Review (MDR)
Main Results / Significant Achievements
The PERIOD demonstration objectives have been elicited from the high-level customer needs. Substantiated by programmatic constraints, technical feasibility and market opportunities, they have been translated into detailed mission requirements. A mission architecture has been developed that maps those requirements to mission phases and physical entities.
The mission phases have been aligned in a high-level mission sequence that served as an input for the initial operations planning. Likewise the physical decomposition has been used as an input to the definition of the system concept.
In parallel, also the mission for the payload satellite with its scientific mission has been plotted. The results of the combined Mission Definition process have been formalized in the Mission Description Document and submitted for review during the Mission Definition Review (MDR).
What is next
In the next iteration of the Mission Description the findings from the MDR will be implemented. Based on this update the system requirements will be adapted and flown down to the next level of decomposition.
Throughout the development of the PERIOD demonstration the MDD will be kept up-to-date and continue to serve as a reference for the technical design.
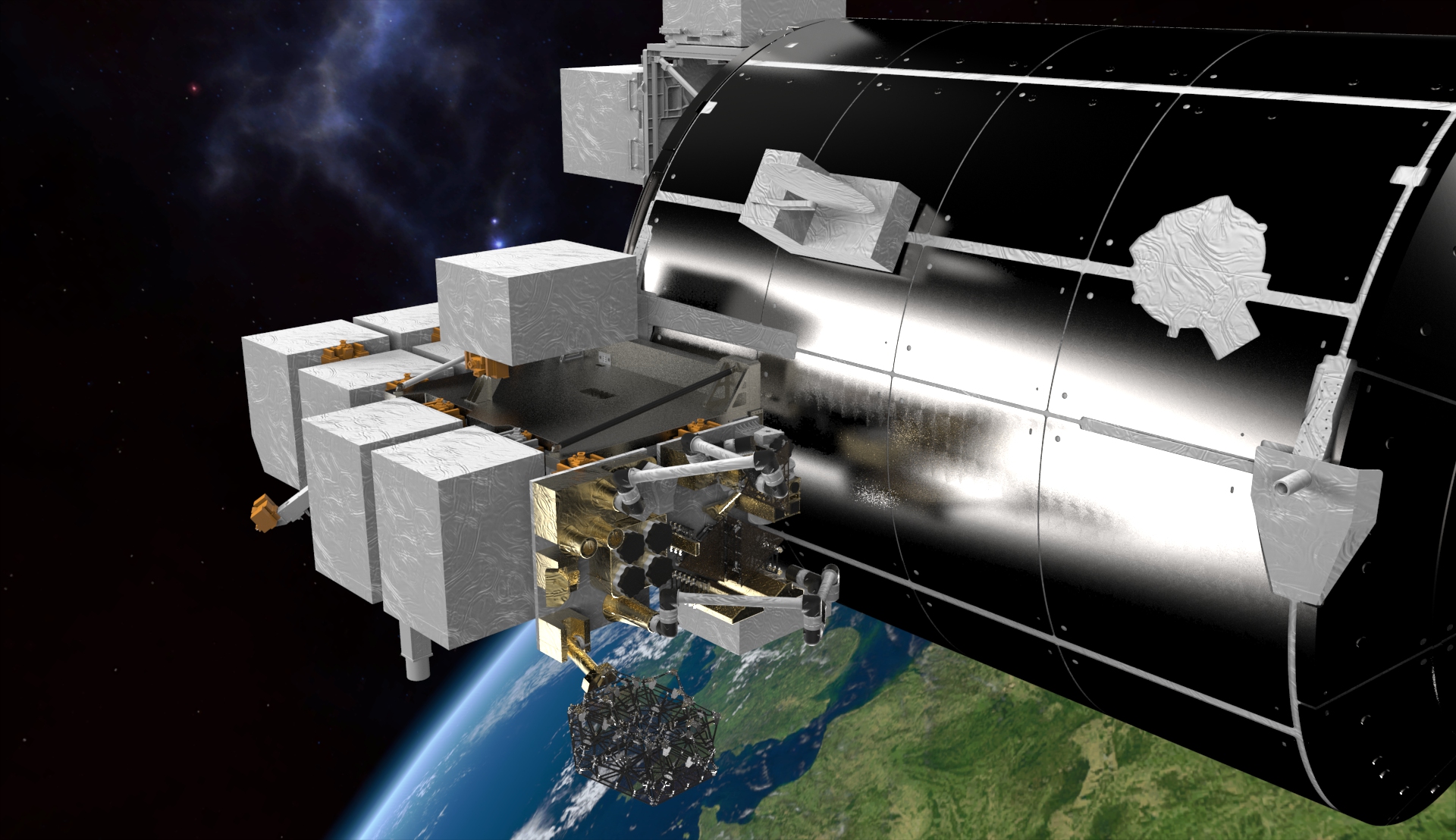
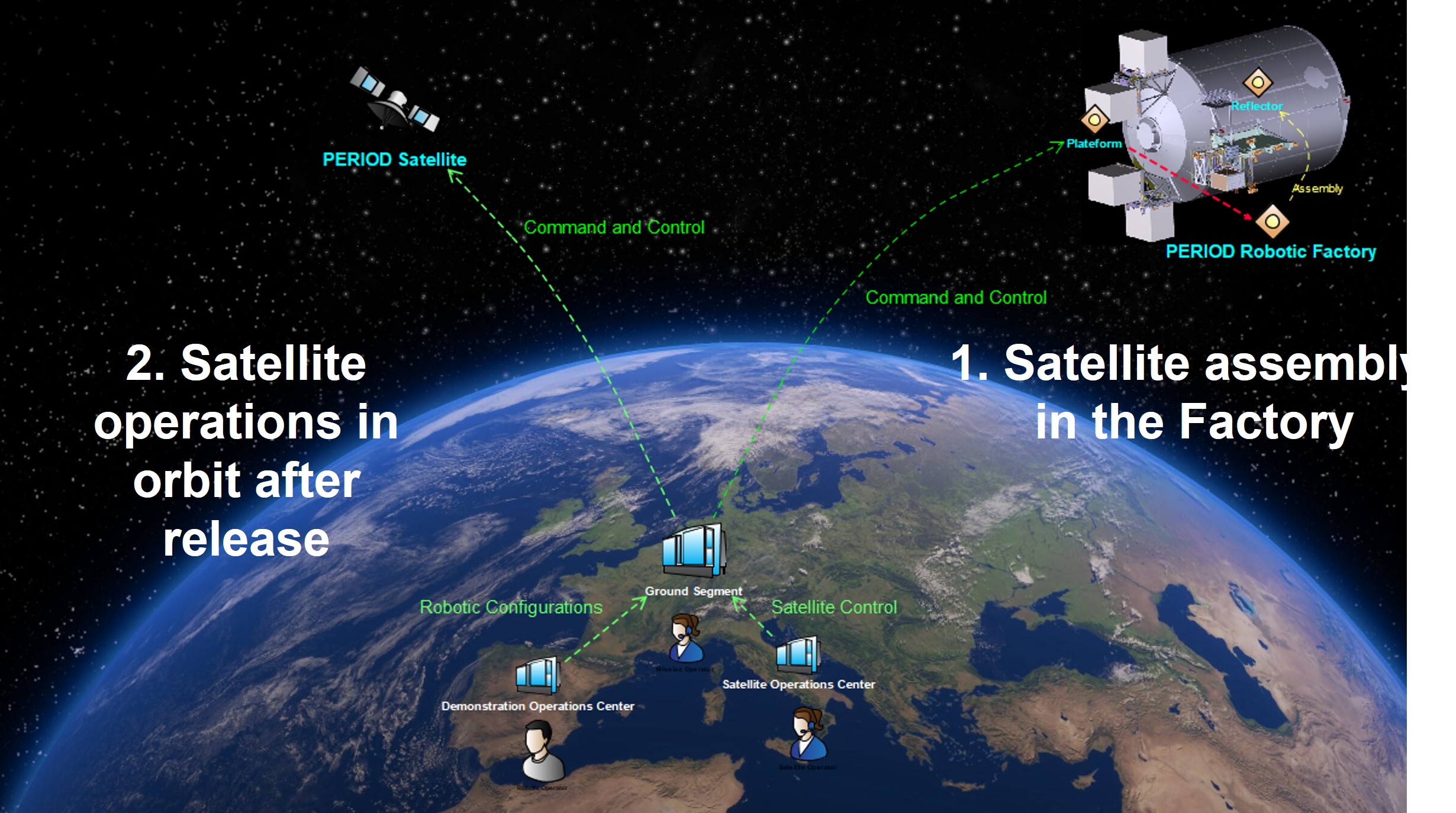
Highlights Summary
The PERIOD demonstration mission definition has been refined and presented at the Preliminary Requirements Review (PRR) and different workshops and conferences.
Main Results / Significant Achievements
The mission definition was actualized with a refinement of the mission phases and the definition of the overall mission architecture concept. For each of the main demonstration phases, the more detailed operations including the interactions between the operational entities were described in the MBSE mission model. In addition, the mission definition has undergone a value analysis to assess the key requirements and main system functions w.r.t. the product and cost breakdowns. The overall costing of the project phases B2/C/D was generated based on the defined system concept and development and verification logic. The definition of the specific scientific mission based on the VLF payload satellite (Very Low Frequency) has been continued for the mission phase coming after the release of the built satellite from the ISS. The results of the combined mission definition, value analysis and costing process have been formalized in the documentation delivered for the Preliminary Requirements Review (PRR).
What is next
In the next project phase a new iteration of the analysis of the mission, operations, functional architecture, logical architecture will be started again taking the PRR findings into account to provide a deeper insight into the overall mission and system concept definition. The definition of the lower level operations and components will be started to provide the next level of decomposition and requirements.
Highlights Summary
The PERIOD demonstration mission definition has been refined and presented at the Preliminary Requirements Review (PRR) and different workshops and conferences.
Main Results / Significant Achievements
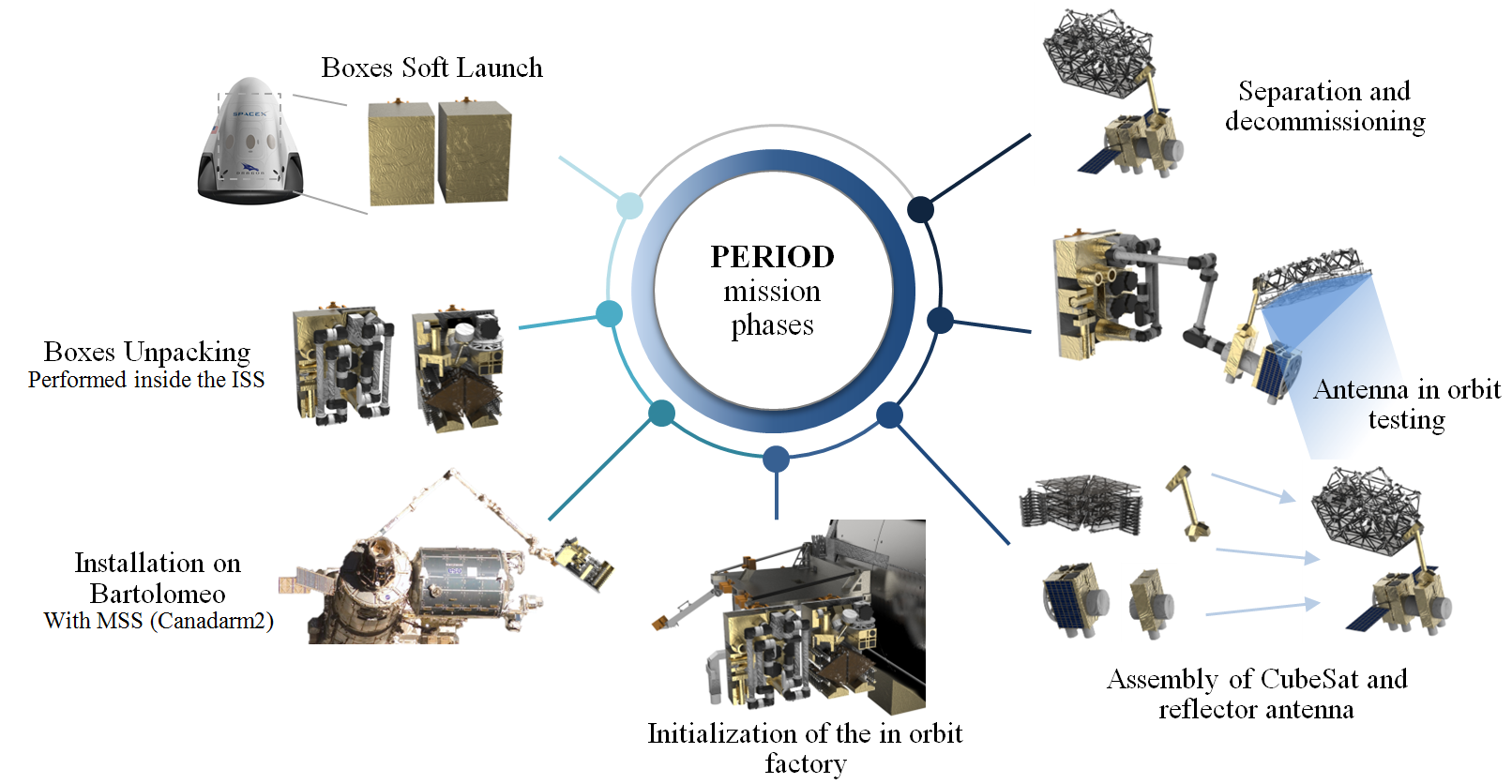
Based on the findings from the Preliminary Requirements Review (PRR), the mission definition was updated, refining the overall mission architecture concept. For each of the main demonstration phases, the operations were defined in more detail, translating the interactions between the operational entities in an updated MBSE model.
The definition of the scientific mission for the VLF payload satellite (Very Low Frequency) has been refined for the free-flight phase after the release of the satellite from the ISS.
What is next
In the next project phase running up the the Systems Requirements Review (SRR) the definition of the lower level operations and components will be continued to provide the next level of decomposition and requirements.
CONCEPT
DEFINITION
AIRBUS Defence and Space GmbH
ContributorsAIRBUS Defence and Space SAS, AIRBUS Defence and Space LTD, GMV, SPACEAPPS, SENER Aeroespacial, DFKI, ISISPACE
02
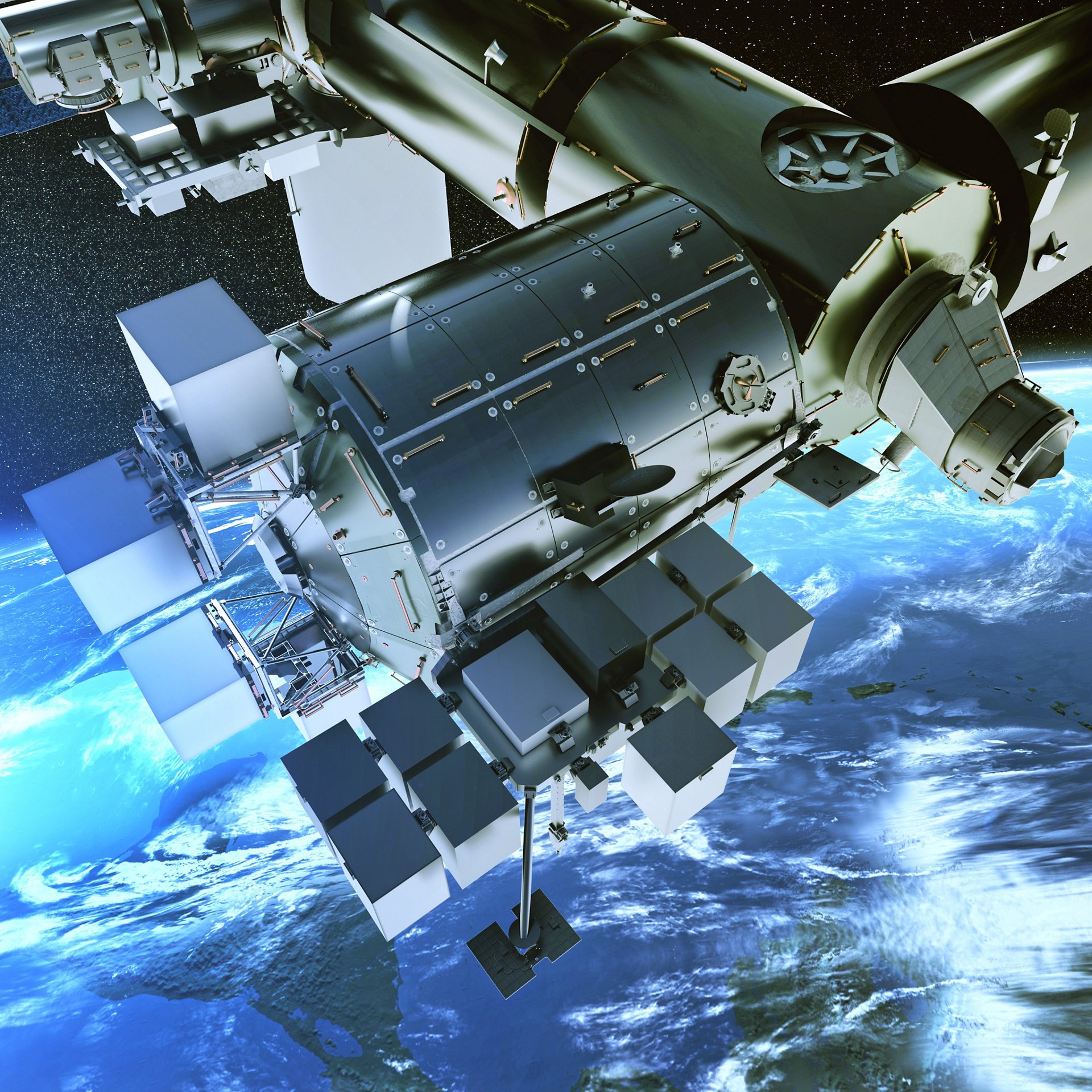
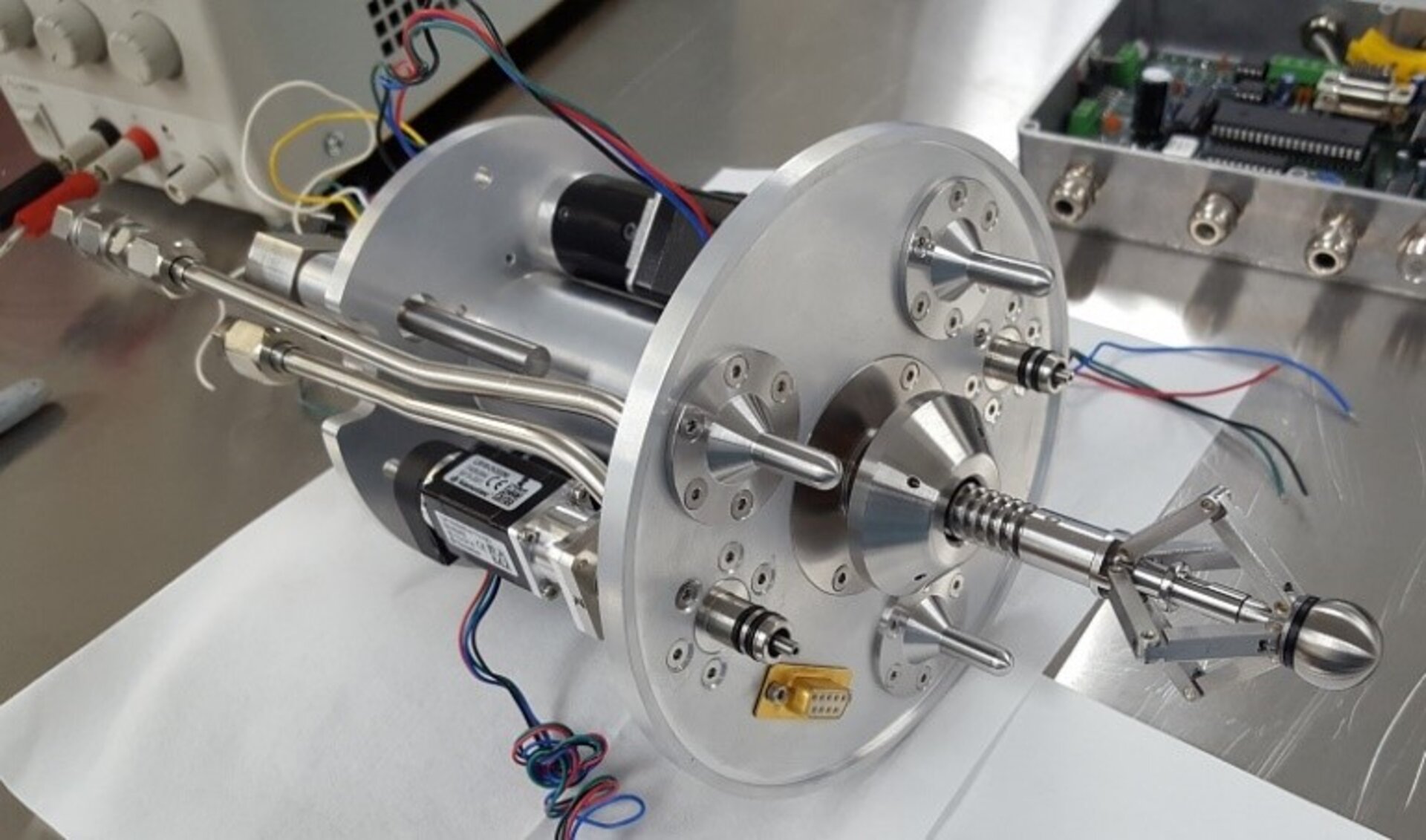
Highlights Summary
As part of the mission definition phase, the initial architecture concept and product tree as well as mission and operation phases have been elaborated with the team utilizing Airbus’ Model-Based Systems Engineering (MBSE) development process and toolchain. The mission phases and system concept were defined using Bartolomeo as the baseline for the platform. Nevertheless, the definition of the architecture, the product tree and the operations also took into account the transferability to other (free-flyer) platforms aiming at implementation of future applications after the demonstration. The detailed PERIOD architecture definition started after MDR with the functional definition and the preparation of trade-off studies for the major technical aspects.
Main Results / Significant Achievements
Bartolomeo provides an excellent environment for initial in-orbit demonstrations (IOD) of the technological capability and feasibility for the OSAM use cases, to prove and evaluate related operational concepts as well as to increase maturity of space robotics technology first used in space. Repeatability of the necessary operations enables evaluation and generate evidence in terms of performance, robustness and success probability. The costs and effort for logistics, infrastructure and other aspects not related to the robotic capabilities can be kept low.
The robotic factory IOD will aim at assembling a small satellite with a large antenna reflector manufactured in space, exchanging payloads of the satellites and performing an attachment and refueling experiments utilizing ASSIST.
The architecture definition, implementing the integration of the SRC building blocks in a robotic factory, is currently ongoing and major trade-off studies are under preparation. The decisions for the system concept are ranging from the number of manipulators to the use of Standard Interconnects down to the software functionality and sharing of control between ground and in orbit execution.
The redundancy concepts for the different subsystems and equipment’s is under specification to meet the overall mission dependability.
The complete architecture definition will be represented in an MBSE environment to model the mission definition, the operational definition, the functional definition and the logical definition in one SysML model.
What is next
In the next steps, the required functions to realize the defined operations and their allocation to the logical and physical elements (subsystems) will be described in the MBSE model and a more detailed design of the factory architecture and the accommodation will be developed. In addition, needed analyses will be carried out with regard to various criteria such as function, structure, electrical, computing power, etc. and the concept is optimized iteratively based on the results and relevant trade-off.
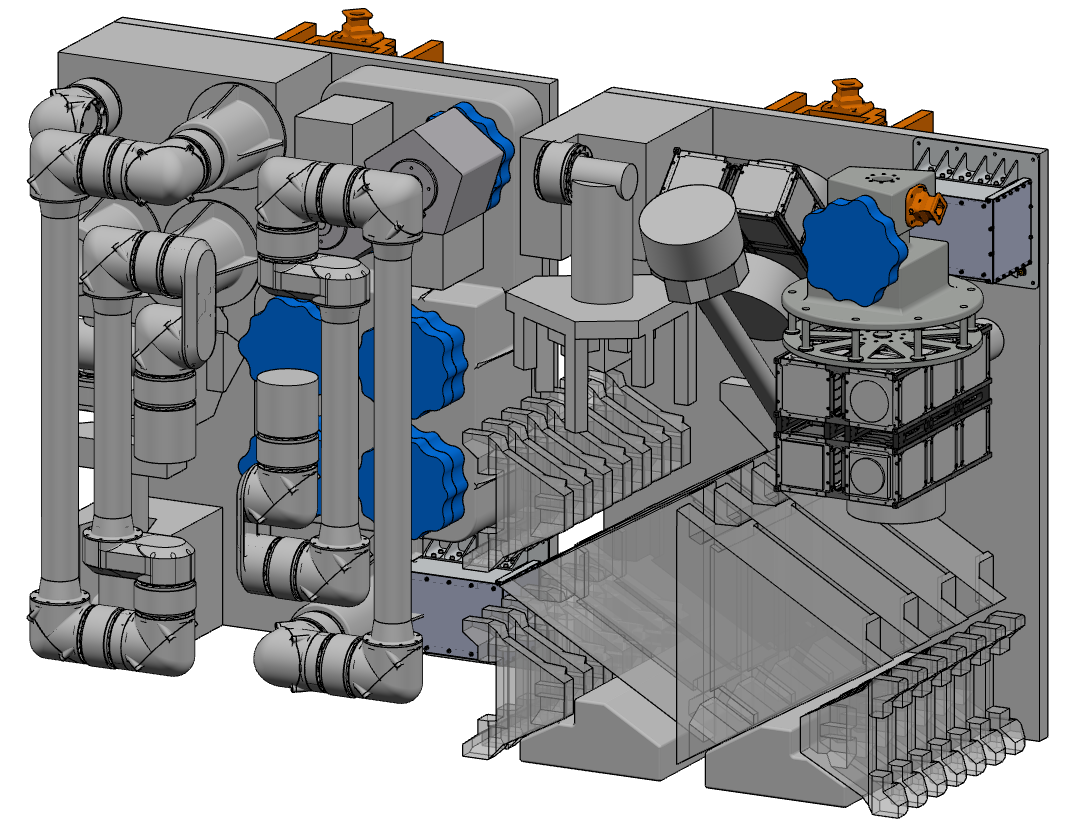
Highlights Summary
Based on the definition of the mission and operation phases the functional analysis was performed and the functional architecture was modelled with the team utilizing Airbus’ Model-Based Systems Engineering (MBSE) development process and toolchain. Several trade-offs and related analysis were performed in parallel to the further refinement of the product tree and requirements definition as well as mapping of the identified needed functions to the logical and physical elements layer of the system model. More detailed designs of the factory architecture and the accommodation were developed as well.
Pre-Development activities of SRC PERASPERA technologies were performed by implementing and testing the specified interfaces between the different software building blocks in order to close identified gaps and further integrate for realization of the defined software architecture to implement (shared-) autonomous control of the robotic factory.
Main Results / Significant Achievements
The architecture and accommodation of the orbital factory to be commissioned on Bartolomeo in order to demonstrate the robotic manufacturing and assembly as well as attachment and refueling operations in orbit were defined more in detail. Two neighboring Bartolomeo (https://www.airbus.com/space/space-infrastructures/bartolomeo.html) slots will be used to mount two payload boxes in parallel. The Factory Box will accommodate all robotic technologies to provide the required functionality comprising two manipulators equipped with end-effector cameras and tool exchange interfaces to allow flexible configuration for different tasks. The tools are stored in a magazine and workbench elements serve as holding and alignment devices to support the manufacturing and assembly processes. The robot control unit interfacing to all robotic devices and executing the control software to perform autonomous operations is also hosted in the Factory Box.
The Satellite Kit Box will be mounted in the neighboring Bartolomeo slot and contains all elements of satellite and reflector to be manufactured and assembled mounted in dispensers and storages. After testing and deploying the assembled satellite the Satellite Kit Box will be exchanged by a third box, the Refueling Box, which Implements an attachment and refueling experiment which will also be operated by the robotic system accommodated in the Factory Box.
Design decisions such as how many manipulators are required in the factory and which connections of the satellite to be assembled will be established utilizing a Standard Interconnect or a specific mechanism and dedicated tooling have been taken based on results of performed analyses and trade-offs.
What is next
In the next steps, the architecture definition and interface specification, which was so far mainly concentrating on the external ones, as well as requirements to the subsystems will be defined more in detail based on analyses with regard to various criteria such as function, structure, electrical, computing power, thermal, performance, etc.
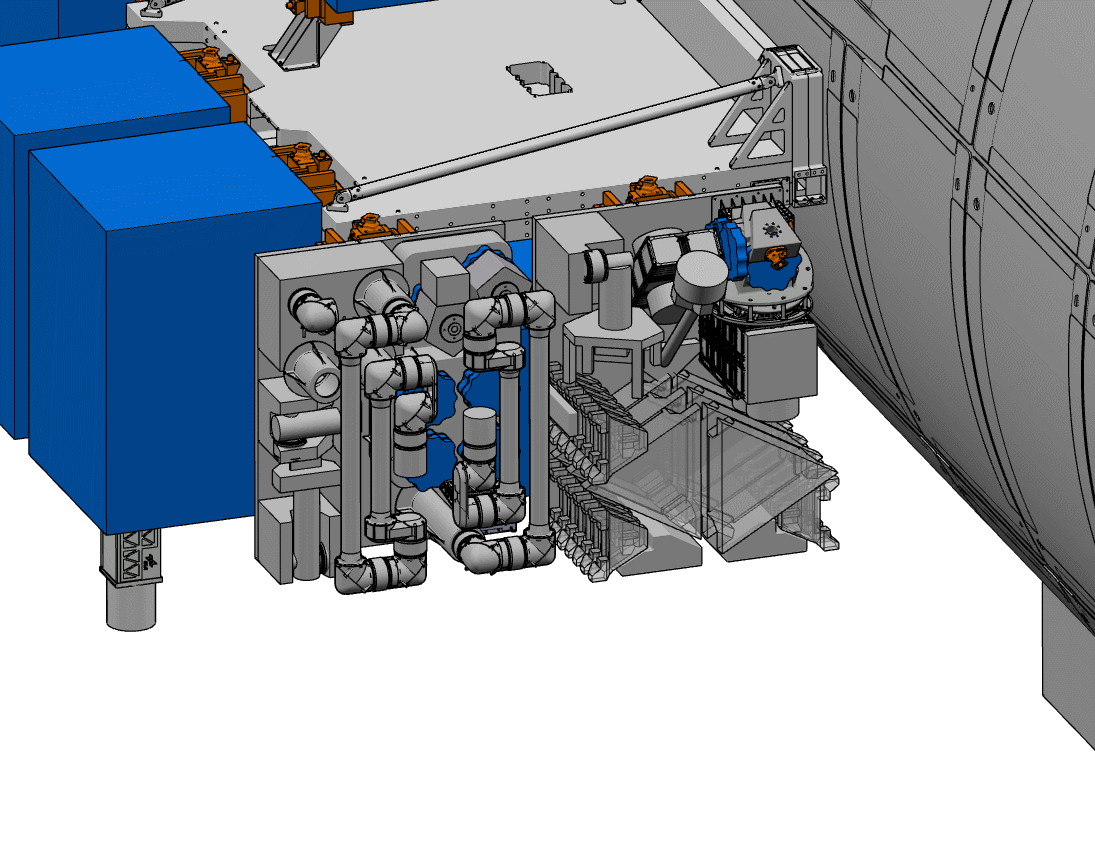
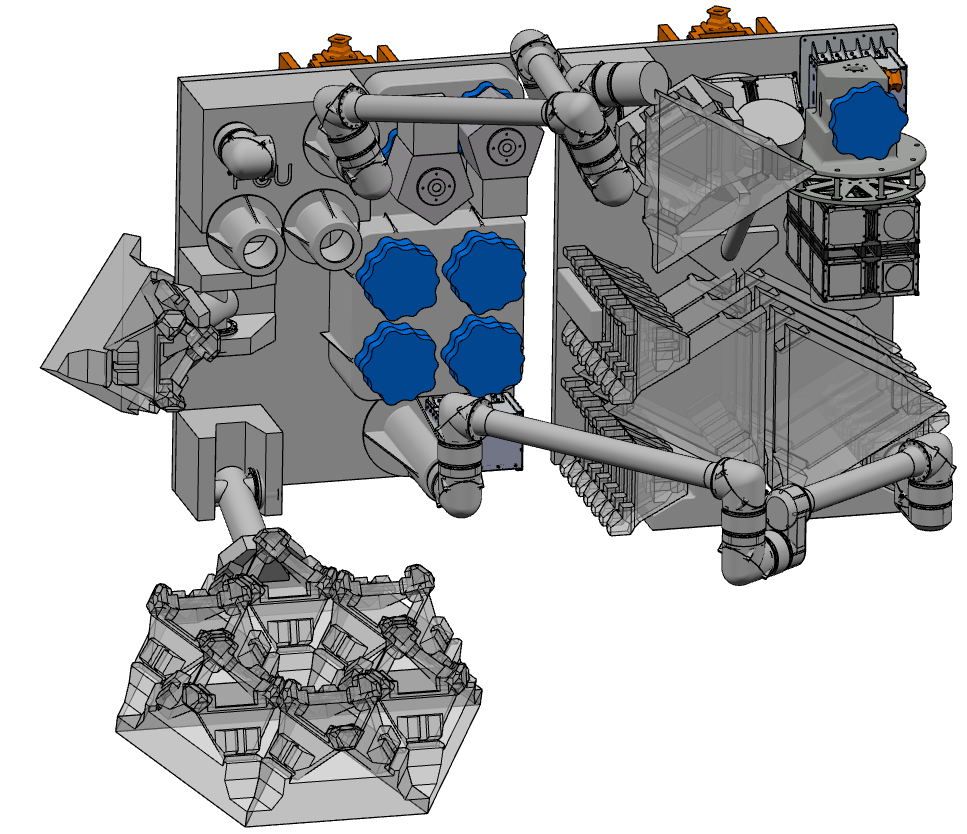
Highlights Summary
The concept definition of the system used for the PERIOD demonstration has progressed a lot by harmonizing the individual building blocks in terms of mechanical, electrical and data interfaces and on the other hand by the accommodation of all the components within the available design space of the Bartolomeo payload boxes.
Main Results / Significant Achievements
The PERIOD system is a complex robotic system consisting of several hardware and software building blocks. The harmonization of those building blocks is one of the major tasks for the system concept definition. The individual architects for functional chains worked together to achieve this objective and to establish trade-offs to select the most suitable baseline. For some of the components it is necessary to adapt the current design slightly to fit to the overall concept. Especially the complex robotic operations required special attention as it is necessary to simulate the robotic motions to ensure that the mechanical accommodation does allow the robot to reach all points with the required orientation. The challenge is to minimize the iterations as each check in the simulation requires an exhaustive preparation of the simulation model. The building blocks are developed in parallel, either within PERIOD or in separate activities which requires special care that all items are harmonized and the latest update considered for accommodation and simulation.
What is next
The next steps are the final definition of the operations after minor modifications in the baseline, the generation of the final CAD file for SRR and the last updates of the requirement specification due to evolved baseline and building blocks.
TECHNOLOGY
DEVELOPMENT
DFKI
ContributorsAIRBUS Defence and Space GmbH, GMV, SPACEAPPS, SENER Aeroespacial, ISISPACE
03
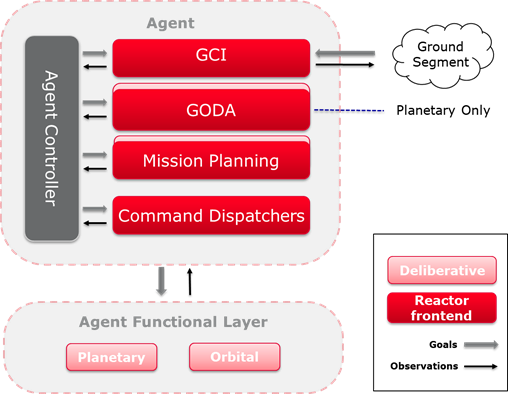
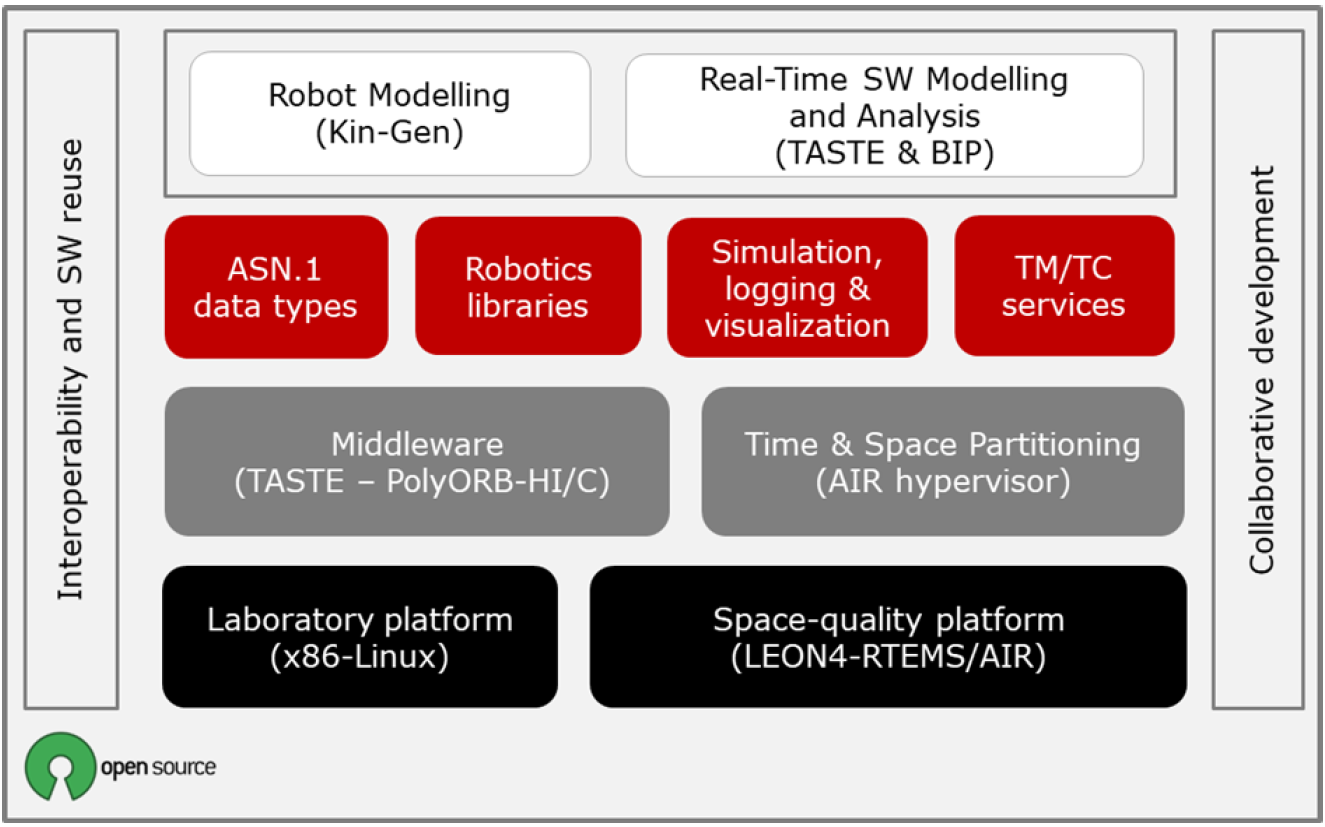
Highlights Summary
The overall objective of this activity is to increase the maturity of core software components and prepare them for an in-orbit demonstration mission. To this aim in the first phase of the project the core software technologies (i.e., ESROCOS, ERGO, InFuse, I3DS) were evaluated with respect to the existing technical requirements and their further developments identified to advance their implementations to technology readiness level five (TRL 5).
Main Results / Significant Achievements
The main results of the activity achieved till the Mission Definition Review consist out of a) providing a reference document for space software development and evaluation, b) specifying an overview of the reference implementations of core (software) building blocks (i.e., ESROCOS, ERGO, InFuse, I3DS), c) illustrating available capabilities in an early demonstration scenario, d) identifying implementation gaps of the reference implementations with respect to the performance requirements, e) defining further development activities to close identified implementation gaps and advance the building blocks to TRL 5.
The identified procedures for space software development and evaluation rely heavily on a set of European Space Standards of the European Cooperation for Space Standardization (ECSS) as well as the software development guidelines defined by the Motor Industry Software Reliability Association (MISRA), i.e., MISRA C and MISRA C++.
What is next
Next steps of the activity planned till the Preliminary Design Review (PDR) will involve in the first place the refinement of the already identified gaps and technical requirements of the building blocks. The implementation phase will follow to close the identified gaps and advance the software in question till TRL5. At the same time, the test and validation plan will be prepared that will be used after the PDR to perform the technology readiness assessment (TRA) of the involved software building blocks.
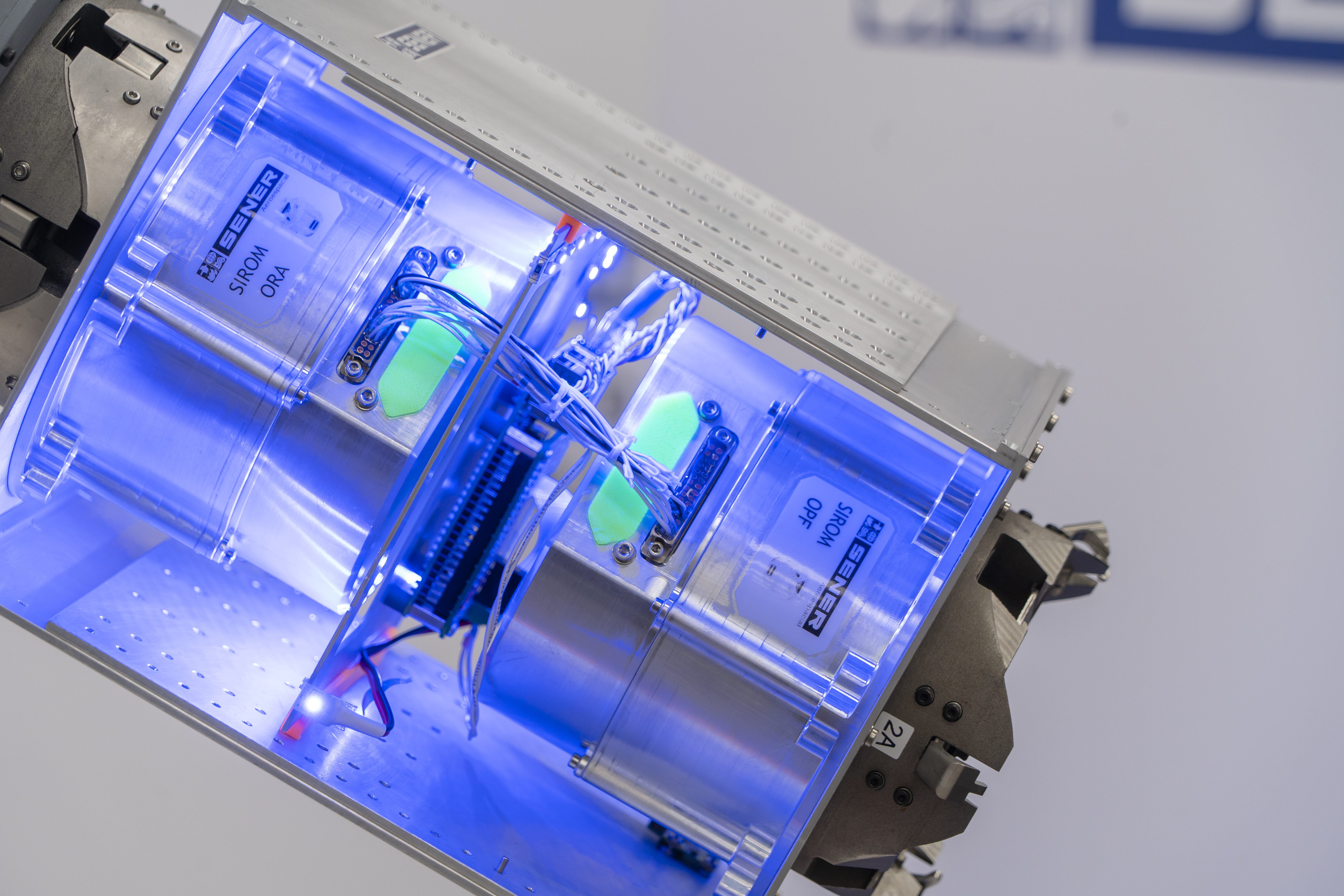
Highlights Summary
The overall objective of this activity is to increase the maturity of core software components and prepare them for an in-orbit demonstration mission. To this aim in the second phase of the project the core software technologies (i.e., ESROCOS, ERGO, InFuse, I3DS) were further developed to close the identified gaps in the first phase of the project and a test and validation plan to be performed on a breadboard was drafted in detail.
Main Results / Significant Achievements
The main results of the activity achieved till the Preliminary Requirements Review (PRR) consist out of a) implementation of further development activities to close identified implementation gaps and advance the building blocks to TRL 5, b) drafting of a test and validation plan of the building blocks to evaluate their technology readiness assessment (TRA) and validate their usage with respect to the envisioned technical specification of the project.
The drafted test and validation plan described is based on the ECSS-E-ST-40C standard which has been tailored/adapted for the specific characteristics and constraints of the PERIOD project. To this end the document integrates the software (unit/integration) test plan, software validation plan as well as software validation specification.
What is next
Next steps of the activity planned till the System Requirements Review (SRR) will involve in the first-place further implementation of building blocks to close the remaining gaps and advance the software in question till TRL 5. At the same time, the testing phase will be initiated according to the defined test and validation plan to assure that the pre-development software is ready to be integrated onto the envisioned breadboard. Finally, the software validation phase will follow and will conclude with the assessed TRL of the software building blocks.
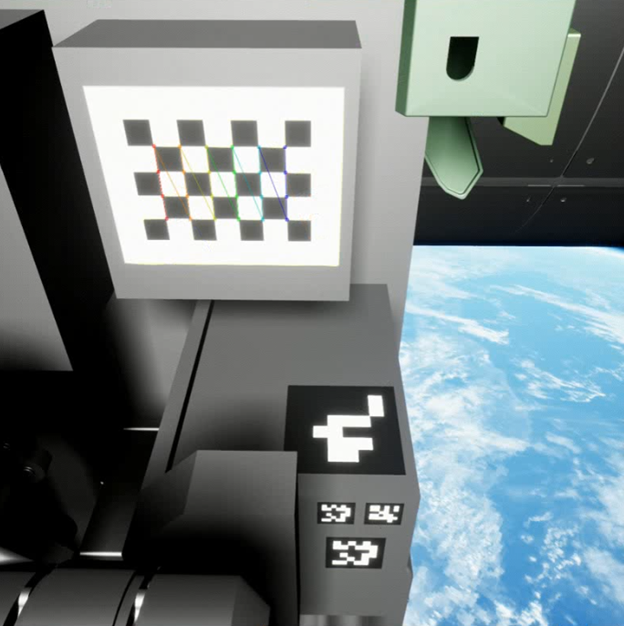
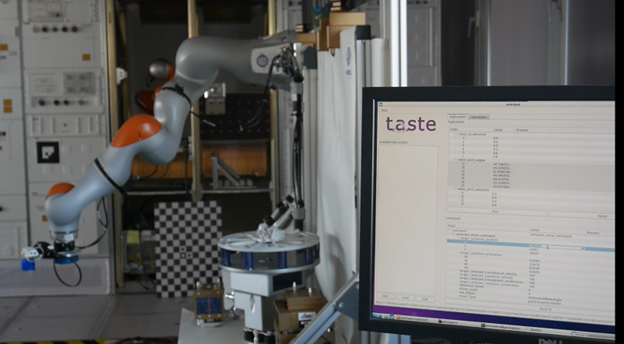
Highlights Summary
The overall objective of this activity is to increase the maturity of core software components and prepare them for an in-orbit demonstration mission. To this aim in the second phase of the project the core software technologies (i.e., ESROCOS, ERGO, InFuse, I3DS) were further developed and tested to close the identified gaps in the first phase of the project following the test and validation plan defined in the first project phase (2021).
Main Results / Significant Achievements
The main results of the activity achieved since the Preliminary Requirements Review (PRR), held in December 2021, are related to the software technology building blocks' refinement and their local integration with each other using simulation tools. During the local integration testing using the simulator, new gaps were identified which were successfully implemented and integrated again between the building blocks involved.
Along the way, it was identified the predefined Test and Validation Plan, produced in the previous project phase (2021), needs to be also refined for better support of the technology readiness assessment (TRA) at the end of the project.
What is next
Next steps of the activity planned till the System Requirements Review (SRR) will involve, in the first place, finalizing the local integration testing of all software components using the simulator. When done, the software must be deployed, tested, and integrated into a relevant operational environment (RISMAT).
Finally, the execution and analysis of the demonstration use-cases results will be used for the TRL software building blocks assessment.
CHALLENGES AND
OPPORTUNITIES
AIRBUS Defence and Space GmbH
ContributorsAIRBUS Defence and Space SAS, AIRBUS Defence and Space LTD, EASN-TIS, GMV, SPACEAPPS, SENER Aeroespacial, DFKI, ISISPACE
04
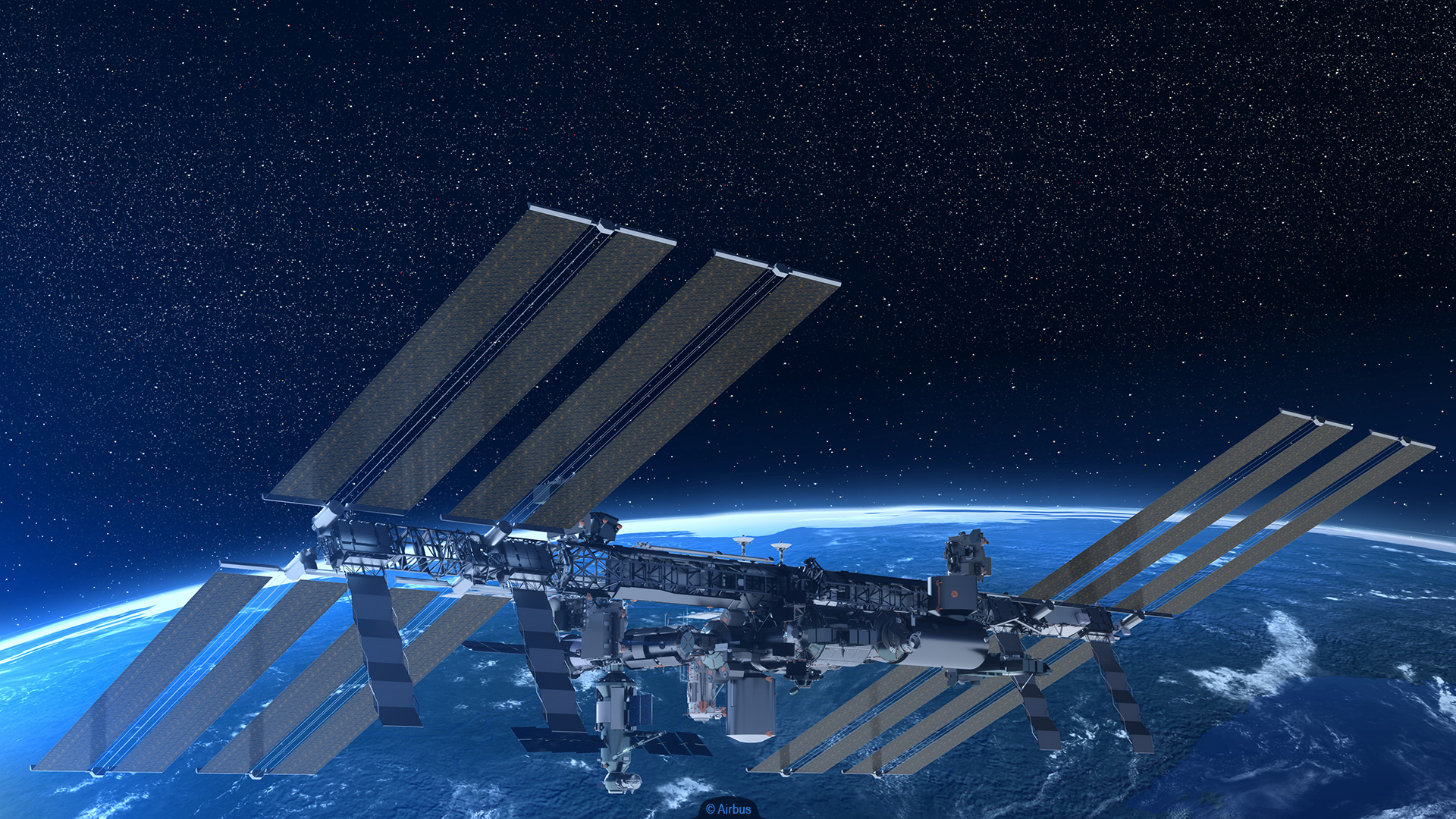
Highlights Summary
The implementation of the highly complex PERIOD demonstration will provide a great opportunity to offer a new range of products and services to the potential customers. On the other hand the complexity of this project is also a great challenge.
Main Results / Significant Achievements
PERIOD will integrate many difficult tasks from the In-Space Manufacturing and Assembly (ISMA) domain. Each one of them requires the development of dedicated demonstration kits, tools, skills and operational procedures. And all of these constituents need to be safe, dependable and resilient in their work environment. Thus a large challenge is the integration of those elements into a working system.
Due to the remoteness of space being one key aspect in the future utilization of the system, a high level of autonomy will already be implemented in the demonstration mission.
If the ISMA activities will be successfully demonstrated within the scope of the PERIOD demonstration, this could be an enabling factor to a possibly large commercial market.
What is next
One of the next challenges to be tackled would be the logical integration of PERIOD on the Bartolomeo Platform attached to the ISS. It should be demonstrated that the PERIOD operations can be performed within the constraints of the platform. The most important aspects will be the safety of the crew in extravehicular activities (spacewalks) and avoiding any disturbance of the ongoing ISS operations.
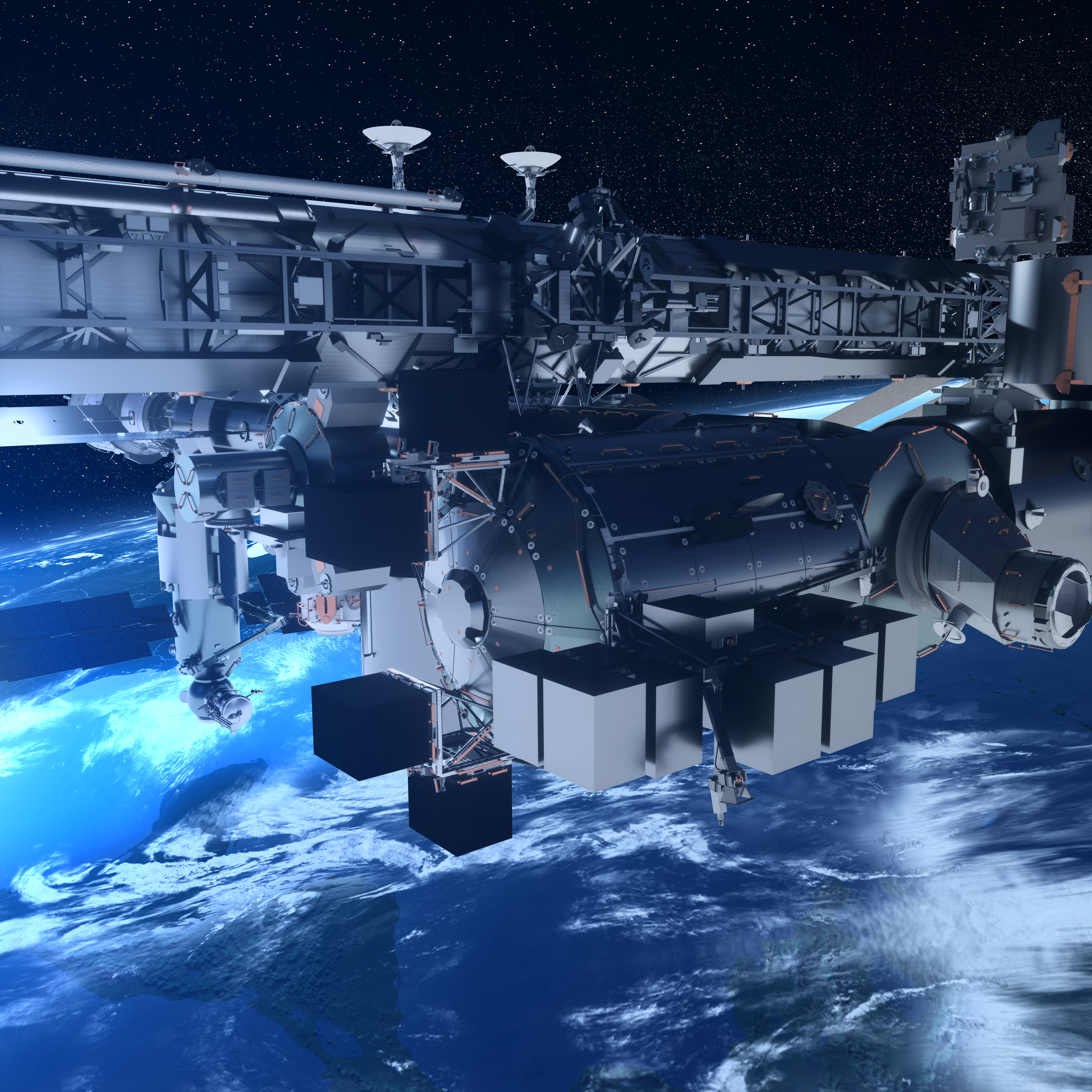
© AIRBUS
Highlights Summary
The implementation of the highly complex PERIOD demonstration will provide a great opportunity to offer a new class of disruptive products and services to the potential customers. The complexity of this project is also a great challenge allowing to advance on the robotic and autonomy technology development applicable to a wide range of space applications.
Main Results / Significant Achievements
PERIOD will integrate many complex tasks from the In-Space Manufacturing and Assembly (ISMA) domain like the manufacturing of reflectors and satellites, as well as their reconfiguration, maintenance and inspection. Each one of them requires the development of dedicated demonstration boxes, tools, skills and operational procedures. And all of these constituents need to be safe, dependable and resilient in their work environment. Thus, the challenges are the development and verification of all those single robotic and autonomy technologies and also their integration into a working and coherent system operated in Earth orbit.
Due to the remoteness of space being one key aspect in the future utilization of the system, a high level of autonomy will already be implemented in the demonstration mission. If the ISMA activities will be successfully demonstrated within the scope of the PERIOD demonstration, this will be an enabling factor to a possibly large commercial market.
What is next
One of the next challenges to be tackled would be the logical integration of PERIOD on the Bartolomeo Platform attached to the ISS. It will be demonstrated that the PERIOD manufacturing and assembly operations can be performed in these real space conditions wrt micro-gravity, temperature, radiation and illumination.
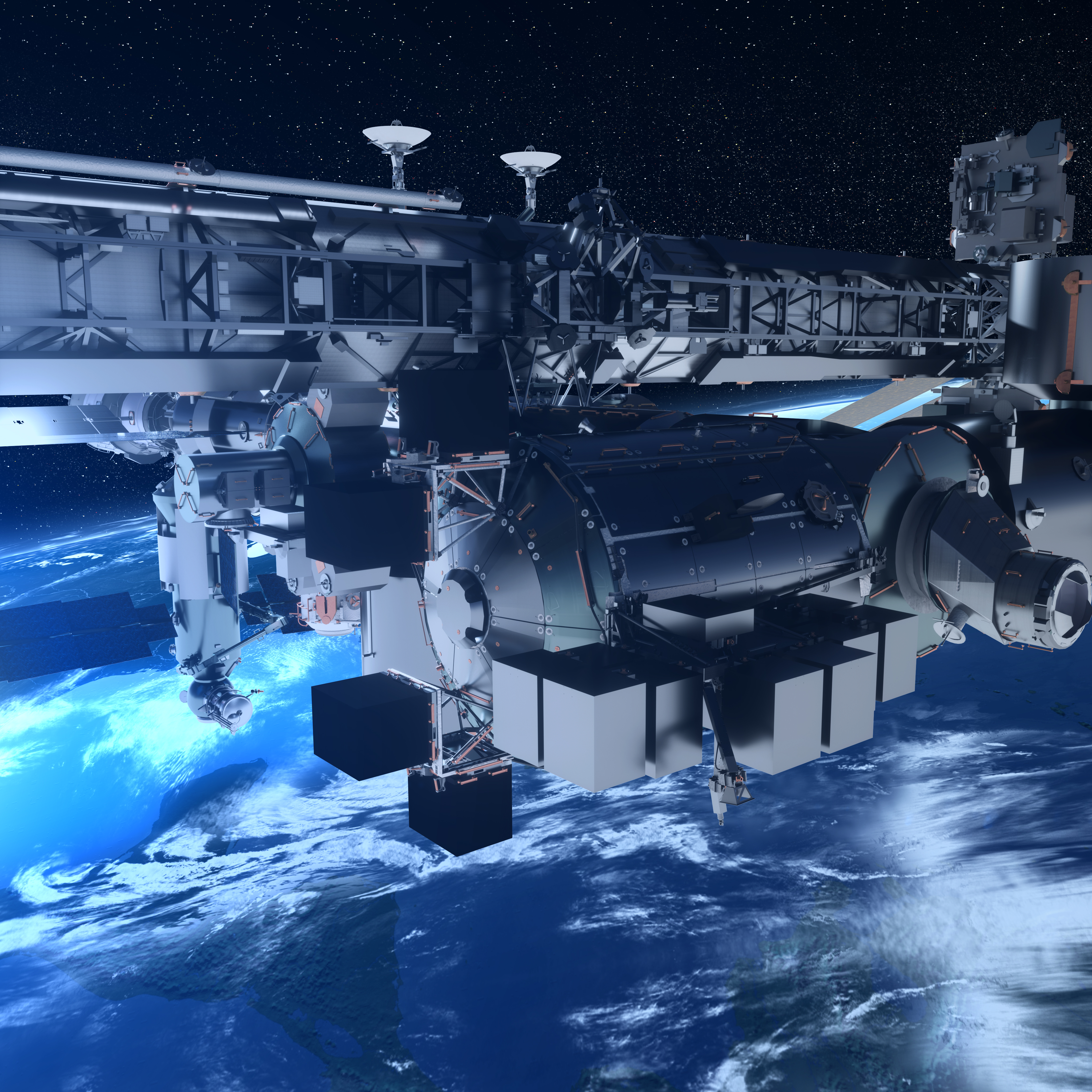
Highlights Summary
The implementation of the highly complex PERIOD demonstration will provide a great opportunity to offer a new class of disruptive products and services to the potential customers. The complexity of this project is also a great challenge allowing to advance on the robotic and autonomy technology development applicable to a wide range of space applications.
Main Results / Significant Achievements
PERIOD will integrate many complex tasks from the In-Space Manufacturing and Assembly (ISMA) domain like the manufacturing of reflectors and satellites, as well as their reconfiguration, maintenance and inspection. Each one of them requires the development of dedicated demonstration hardware, tools, skills and operational procedures. And all of these constituents need to be safe, dependable and resilient in their work environment. Thus, the challenges are the development and verification of all those single robotic and autonomy technologies and also their integration into a working and coherent system operated in Earth orbit.
Due to the remoteness of space being one key aspect in the future utilization of the system, a high level of autonomy will already be implemented in the demonstration mission. If the ISMA activities will be successfully demonstrated within the scope of the PERIOD demonstration, this will be an enabling factor to a possibly large commercial market.
The integration of PERIOD into the infrastructure of the International Space Station is one of the challenges that come as normal work in any ISS project. Currently not only the physical accommodation is being aligned, but also operations, data and power networks or the logistics aspects need to be proactively managed.
What is next
In the next steps the physical environment and requirements imposed by the Bartolomeo platform need to be mapped to the capabilities of our design, in order to ensure the necessary compatibility between the systems.